Stark Varg Motor Technology and Performance Deep Dive in 2025
For decades, the roar of the internal combustion engine has defined the limits of performance and possibility on the motocross track. But a new current is surging through the world of motorsports, a silent revolution promising to redefine power, control, and the very essence of riding.
We’re not just talking about swapping gas for electrons, but about a fundamental shift in how we experience the thrill of acceleration, the grip of the tires, and the connection between rider and machine.
Forget incremental improvements; prepare to witness a leap into the future as we dissect the beating heart of the Stark Varg: its electric motor.
This isn’t just an engine replacement; it’s a meticulously engineered marvel designed to unleash a new paradigm of performance.
Let’s delve into the technologies and innovations that make this motor a game-changer, and explore how it’s poised to electrify the future of motocross.
This is where power meets precision, and the silent surge of innovation takes center stage.
Learn about: Stark Varg EX Is This the Ultimate Electric Dirt Bike in 2025
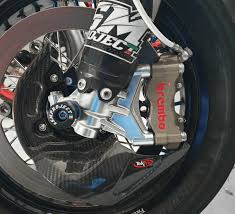
How does the Stark Varg Motor compare to a traditional 450cc combustion engine in terms of torque?
This is a great question! Here’s a breakdown of how the Stark Varg’s motor’s torque compares to a traditional 450cc combustion engine, focusing on key differences and performance implications:
Stark Varg Motor Torque Characteristics:
-
Instant Torque Delivery: Electric motors are known for their ability to deliver maximum torque almost instantly from 0 RPM. This is a huge advantage compared to internal combustion engines. The Stark Varg motor leverages this to its full potential.
-
Higher Peak Torque (Likely): While Stark Future doesn’t explicitly state torque figures that I can find in official documentation, it’s generally understood that high-performance electric motors typically exceed the peak torque output of a 450cc ICE. The peak torque on a 450cc varies between around 35-45 Nm (26-33 lb-ft). Given the claimed horsepower, it’s very likely the Stark Varg motor exceeds this.
-
Wide Torque Curve: Electric motors provide a very flat and wide torque curve. This means the motor produces high torque over a broad RPM range. The Stark Varg benefits from a very usable power band. You can get significant torque virtually anywhere in its operational range.
-
Adjustable Torque Mapping: The Stark Varg features customizable ride modes that allow riders to tailor the torque output. This provides flexibility for different track conditions and riding styles.
stark varg 80hp top speed The Future of Motocross Speed in 2025
450cc Combustion Engine Torque Characteristics:
-
Torque Build-up: 450cc engines require the engine to rev up to a certain RPM before they reach their peak torque. There’s a lag between throttle input and peak torque delivery.
-
Lower Peak Torque (Likely): As mentioned above, peak torque figures on most 450cc engines are generally between 35-45 Nm (26-33 lb-ft).
-
Narrower Torque Curve: 450cc engines typically have a narrower torque curve. Torque output drops off more significantly as the RPMs increase past the peak. This necessitates more frequent gear changes to stay within the optimal power band.
-
Fixed Torque Curve (mostly): While some modern 450s offer multiple engine maps, the fundamental torque curve shape is determined by the engine’s design (cam profiles, porting, etc.)
Stark Varg Dirt Bike The Future of Electric Motocross 2025
Comparison Summary:
Feature | Stark Varg Motor | 450cc Combustion Engine |
Torque Delivery | Instant, from 0 RPM | Requires revving up, lag between throttle and peak torque |
Peak Torque | Higher Peak Torque (Likely) | Slightly Lower Peak Torque (Likely) |
Torque Curve | Wide and flat, consistent power across RPMs | Narrower, torque drops off more quickly |
Adjustability | Highly adjustable torque mapping via ride modes | Limited engine mapping, fixed torque curve shape |
Implications:
-
Stark Varg: The instant and strong torque gives the Stark Varg incredible acceleration and responsiveness. This translates to quicker launches, easier hill climbs, and the ability to pull out of corners with more force. The wide torque curve also means fewer gear changes.
-
450cc: While 450cc engines can be powerful, their torque delivery requires more rider skill to manage. Riders need to be precise with their throttle and gear selection to stay in the optimal power band.
In conclusion: The Stark Varg’s motor offers a significant advantage in terms of torque delivery and overall torque characteristics compared to a traditional 450cc combustion engine. The instant, high torque and wide powerband contribute to superior acceleration, responsiveness, and ease of riding. However, without specific dyno figures from Stark Future, this comparison is based on the general characteristics of electric motors and internal combustion engines in this power range.
Stark Varg Price What You Need to Know Before You Buy 2025
What type of motor controller is used in the Stark Varg?
Unfortunately, Stark Future is not entirely transparent about the specifics of the motor controller used in the Varg. They haven’t released detailed technical specifications or model numbers. However, we can infer some key characteristics and likely features based on the bike’s performance and the general state-of-the-art in electric vehicle technology:
Likely Characteristics of the Stark Varg Motor Controller:
High Voltage System:
Given the claimed power output (80 HP / 60 kW), the Stark Varg likely operates at a relatively high voltage (likely in the 300-450V range). The motor controller needs to handle this high voltage safely and efficiently.
Field-Oriented Control (FOC):
Modern high-performance electric motors almost universally utilize Field-Oriented Control (FOC). FOC provides precise control over the motor’s torque and speed, resulting in smooth and efficient power delivery. It’s highly probable that the Stark Varg’s controller uses FOC.
High Switching Frequency:
The controller likely uses a high switching frequency to minimize current ripple and improve motor efficiency. This also helps reduce noise and vibration.
Advanced Algorithms:
The controller probably incorporates advanced algorithms for:
-
-
Traction Control: To prevent wheelspin and maintain optimal traction.
-
Regenerative Braking: To recover energy during deceleration and braking.
-
Thermal Management: To monitor and control the motor and battery temperatures.
-
CAN Bus Communication:
A CAN (Controller Area Network) bus is likely used for communication between the motor controller, battery management system (BMS), throttle, display, and other electronic components.
MOSFET or IGBT Power Switches:
The power stage of the motor controller likely uses high-performance MOSFET (Metal-Oxide-Semiconductor Field-Effect Transistor) or IGBT (Insulated Gate Bipolar Transistor) switches to efficiently control the flow of current to the motor windings.
Stark Varg Top Speed The End of Gasoline’s Reign? 2025
In Summary:
While we don’t know the exact manufacturer or model of the Stark Varg motor controller, we can confidently assume it’s a sophisticated, high-performance unit that incorporates FOC, operates at high voltage, and includes advanced algorithms for traction control, regenerative braking, and thermal management. It’s designed to maximize the motor’s performance and provide a smooth, predictable, and safe riding experience.
The fact that Stark Future allows for customizable ride modes and power delivery suggests a programmable controller, which allows users to fine-tune the bike’s performance characteristics to their liking.
What are the key features of the motor that contribute to its light weight?
This is another excellent question! While concrete details are limited, we can infer several key features of the Stark Varg motor design that contribute to its light weight, based on common practices in electric motor design and what Stark Future has emphasized in their marketing:
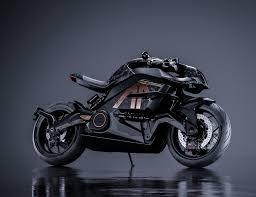
High Power Density Design:
A primary goal in designing motors for electric vehicles (especially motorcycles) is maximizing power density (power-to-weight ratio). This means extracting the most power from the smallest and lightest possible motor. Key design elements include:
-
-
Optimized Motor Topology: Using an optimized motor topology (likely a Permanent Magnet Synchronous Motor – PMSM) that balances power density, efficiency, and cost.
-
Advanced Materials: Utilizing high-strength, lightweight materials such as:
-
High-grade aluminum alloys for the motor housing and end bells.
-
Lightweight composite materials in certain structural components (if feasible).
-
High-performance magnets (e.g., neodymium magnets) with high energy density.
-
-
Optimized Winding Design: Utilizing advanced winding techniques to maximize copper fill factor (the amount of copper packed into the stator slots). This reduces resistive losses and increases torque output without adding unnecessary weight.
-
Kids Motorcycle Fueling Fun and Building Skills in 2025
Integrated Design & Optimized Cooling:
-
-
Compact Integration: Integrating the motor closely with the battery pack and potentially other components (like the inverter/controller) can minimize unnecessary mounting hardware and reduce overall weight.
-
Efficient Cooling System: A well-designed cooling system is crucial for maintaining motor performance and preventing overheating. Efficient cooling allows the motor to operate at higher power levels without adding excessive weight. This could involve:
-
Liquid cooling channels integrated directly into the motor housing.
-
Optimized fin designs for air cooling (if applicable).
-
-
Minimization of Iron Core Mass: Careful design of the stator and rotor iron core is essential to reduce weight. This involves optimizing the core geometry, using thinner laminations, and selecting materials with high saturation flux density to minimize the amount of iron needed.
-
Hollow Shaft Design:
Utilizing a hollow motor shaft design for cable routing and potentially integrating other components inside the shaft can save weight and reduce the overall package size.
Advanced Manufacturing Techniques:
-
-
Precision Machining: Using precision machining techniques to minimize material waste and ensure tight tolerances.
-
Additive Manufacturing (3D Printing): While not confirmed for the Stark Varg motor specifically, additive manufacturing can potentially be used to create complex and lightweight motor components that would be difficult or impossible to produce using traditional manufacturing methods.
-
kids dirt bike 101 Everything Parents Need to Know
In Conclusion:
The light weight of the Stark Varg motor is likely achieved through a combination of factors, including a high power density design, the use of advanced materials, efficient cooling, optimized winding design, and precise manufacturing techniques. Stark Future is focused on creating a high-performance electric motorcycle that is competitive with traditional combustion engine bikes, and minimizing weight is a critical aspect of achieving that goal.
E Ride Pro SS More Than Just an Electric Dirt Bike A Deep Dive